Literature
Titrimetric Determination of the Chlorohydrin Content
3-Chloro-2-hydroxypropyl-N-alkyl-N,N-dimethylammonium chlorides (chlorohydrins) react stoichiometrically with sodium hydroxide to form the corresponding epoxides.
The excess sodium hydroxide is back-titrated with hydrochloric acid and the end point is determined either potentiometrically or through color change of a cresolphthalein indicator solution.
Titrimetric Determination of the Epoxide Content
2,3-Epoxypropyl-N-alkyl-N,N-dimethylammonium chlorides (epoxides) react in aqueous solutions with hydrochloric acid saturated with magnesium chloride to the corresponding chlorohydrins.
The excess acid is back-titrated with sodium hydroxide and the end point is determined either potentiometrically or through color change of a methyl red indicator solution.
Titrimetric Determination of the QUAB Glycol Content
2,3-Dihydroxypropyl-N-alkyl-N,N-dimethylammonium chlorides (glycols) react stoichiometrically with sodium periodate in neutral solution with cleavage of the CC bond to form aldehydes. Epoxide and chlorohydrin remain unchanged under these conditions.
After adding an excess of sodium arsenite, back-titration is accomplished with sodium periodate. The end point is determined either potentiometrically or by means of a potassium iodide/starch solution as indicator.
Determination of Epichlorohydrin (ECH) and 1,3-Dichloropropanol (DCP)
by Gas Chromatography
QUAB reagents may contain epichlorohydrin and 1,3-dichloropropanol at very low concentrations for production-related reasons. The concentration in QUAB is determined by gas chromatography after extraction with diethyl ether.
Epichlorohydrin (ECH)
1,3-Dichloropropanol (DCP)
The calibration is performed by adding ECH/DCP to the QUAB solution being examined.
APHA-Number Determination in QUAB Reagents
QUAB reagent’s APHA-number is measured at the distinction of 436 nm wavelength for color. The measurement is compared to the Platinum/Cobalt Standard APHA 500.
Note: Analysis methods for the above ingredients and for other physical and chemical analysis are available upon request.
Important formulas for cationization of polymers
Theoretical degree of substitution (moles of substituents per moles of anhydro glucose unit):
Cationic nitrogen content (Kjeldahl analysis):
Practical degree of substitution:
Reaction efficiency (yield):
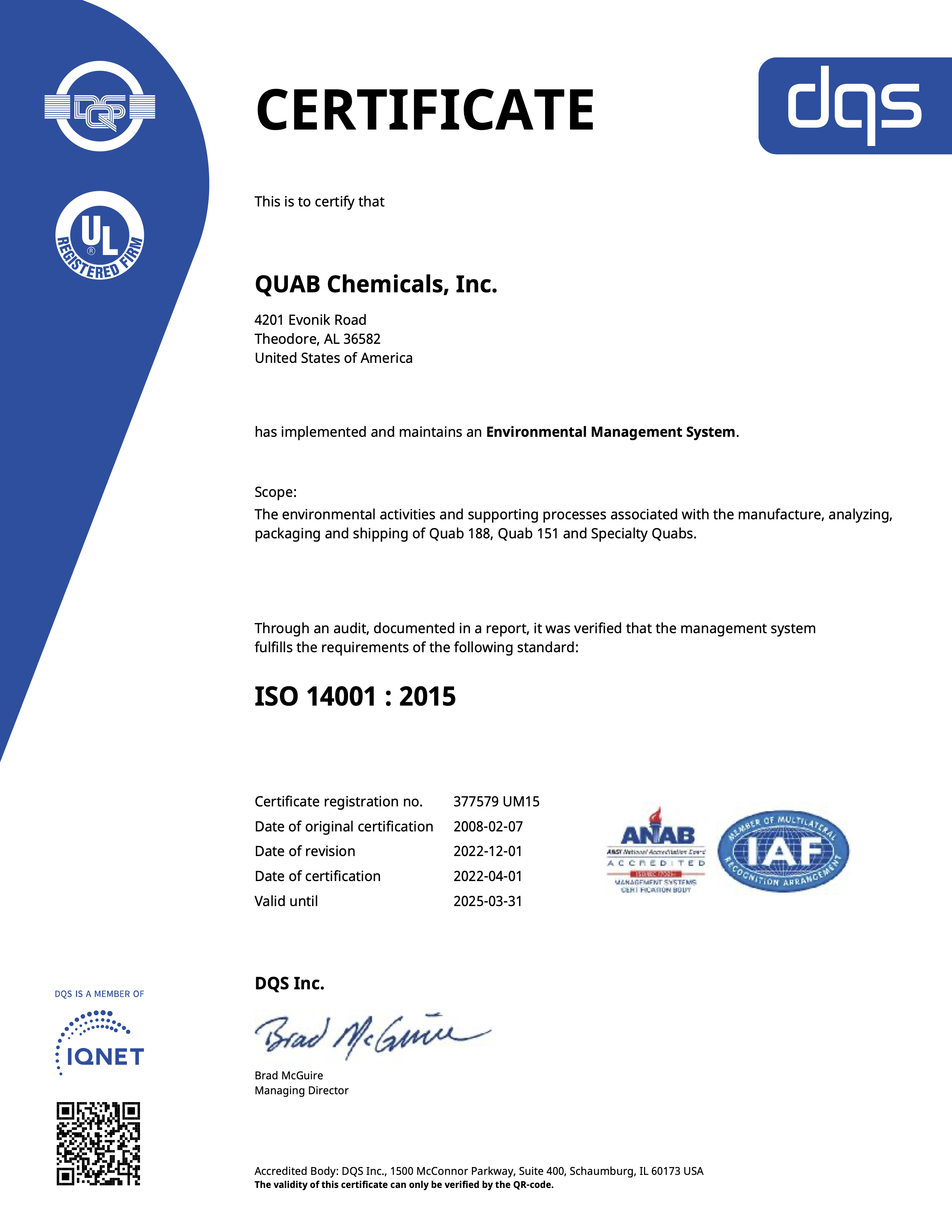
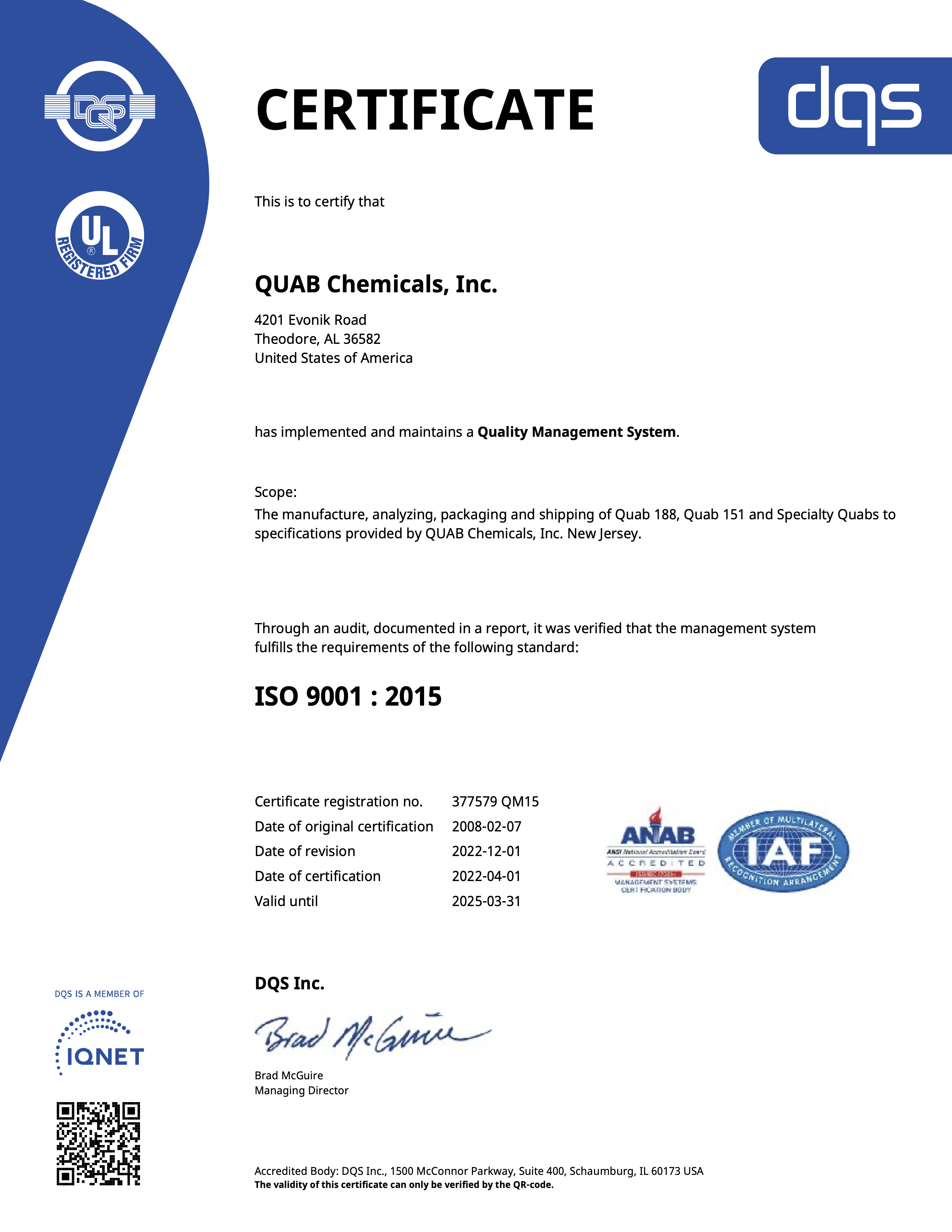
REACH (Registration, Evaluation, Authorisation of Chemicals)
Article 18 Compliance Requirements under REACH for Downstream Users
Over the past two years, we have informed our European QUAB customers that our consortium of producers has unanimously decided to register both CHPTAC (QUAB-188) and EPTAC (QUAB-151) as transported isolated intermediates under REACH. Accordingly, this registration places certain legal obligations on our customers, as downstream users, in regard to the handling and use of the products under strictly controlled conditions (SCC), as specified under Article 18 of the REACH legislation. The REACH regulations compel us to obtain a confirmation from our customers that they understand these obligations.
The decision to register our products as transported isolated intermediates was made for two main reasons: (1) this category best describes how the products are normally sold and used, and (2) selecting a more restrictive category would have involved significantly higher costs for both the producers and for our customers.
We appreciate that many of our customers may find the REACH legislation to be a bit overwhelming and may feel uncomfortable in certifying that they will conform with the Article 18 restrictions for strictly controlled conditions. The purpose of this memo is to try to clarify exactly what these obligations entail.
Our consortium has issued some general guidelines to help you understand these obligations better. To start:
- Every company has the freedom to interpret Article 18 (4) on its own. The supplier does not lay down fixed specifications and will not perform checks.
- If the handling of substances within a company is carried out in accordance with legal regulations, Article 18 (4) should be fully satisfied. The following should be noted:
- -Environmental protection and occupational safety standards established in national law must also be complied with
- -Risk management measures are to be taken into account
- If there are remaining doubts about implementing Article 18 (4). These need to be passed on to the companies’ individual REACH experts for further clarification.
By providing the Article 18 (4) Confirmation to the supplier, the company concerned does not in principle assume a liability risk. Ultimately, an assessment of the contents of the Article 18 (4) Confirmation can only be relevant for the supplier if the purchaser has evidently given a false declaration, i.e. if after considering all conceivable interpretations it is concluded that intermediates are not being handled under strictly controlled conditions. Every planned change in use as an intermediate is to be reported to the supplier.
The following pages include performance guidelines that may help further clarify your obligations under Article 18. The material contained in these guidelines was developed by the QUAS consortium and are not presented with any warranty by SKW QUAB Chemicals, Incorporated. As always, the customer has the ultimate legal responsibility for meeting their obligations under the REACH legislation.
The QUAS Consortium Guidance for the Implementation of Article 18: Requirements for Strictly Controlled Conditions (SCC)
QUAS Consortium procedure for implementing the REACH requirements pursuant to Articles 17 and 18 for on-site isolated intermediates and transported isolated intermediates:
It is generally applicable in the QUAS Consortium Member’s production facilities that they are controlled by instructions, specifications and implementation of rules relating to occupational, plant and environmental safety and that the requirements “strictly controlled” or “rigorously contained” are to be satisfied by each facility at its own responsibility.
The specific measures that are to be taken for the implementation of the conditions (a) to (e) specified according to Article 18 for the strictly controlled handling of intermediates in QUAS Consortium Member’s production facilities are described or listed as examples below:
(a) The substance is rigorously contained by technical means during its whole lifecycle including manufacture, purification, cleaning and maintenance of equipment, sampling, analysis, loading and unloading of equipment or vessels, waste disposal or purification and storage
To satisfy the condition “rigorously contained,” the QUAS Consortium recommends the implementation of a risk-based approach in its production facilities. Based on extensive experience with the handling of hazardous substances, necessary measures are taken to limit exposure to humans and to the environment for the substance in question during normal operations, such that the risk for human health and the environment is minimized.
- The reaction vessel in which the chemical and physical processes take place is to be regarded as “technically sealed” in relation to the surrounding atmosphere in accordance with the current state of the art, i.e. legally prescribed maximum values are not exceeded.
- Handling of substances in facilities with (a) reaction room(s) separated from the surrounding atmosphere or (b) technically equivalent means which prevent release into the surrounding atmosphere (e.g. closed cabin with local exhaust system) is regarded as “rigorously contained”. In accordance with the relevant operating instructions, the plants are usually opened only for a short time.
- The amended version of the German Clean Air Act requires the use of equipment (e.g. pumps) with minimised leakage rates when selecting technical equipment. The satisfactory condition of the plants is ensured by visual inspection, walkabout inspections and suitable technical monitoring devices (measuring and control instruments, safety installations, protective circuits). The exposure of employees, for example, is monitored by means of threshold limit values. Suitable safety measures are taken during sampling and filling procedures (including product removal by suction extraction and product after-treatment).
- Leakage checks are performed, for example, before plant start-up and during the maintenance program.
- Employees wear suitable personal protective equipment in accordance with the operating instructions pursuant to Section 14 of the Hazardous Substances Regulations. This equipment may include full coverage suits with external respirators.
(b) Procedural and control technologies shall be used that minimize emission and any resulting exposure
- Facility-specific safety and environmental protection concepts are in place, which describe the required process and monitoring technologies for the specific processes.
- Measurement and control technology systems which also include protective circuits, as well as trained operators, monitor the proper operation of the plants and prevent the uncontrolled release of substances.
- Wastewater requiring treatment is subjected to pre-treatment as appropriate and transferred to the treatment facility. Separate pipe work/sewage systems are provided for wastewater requiring treatment sent to the treatment plant, and for wastewater not requiring treatment. The wastewater discharge patterns agreed in consultation with the supervisory authorities are monitored within the facility. Both feed and discharge streams from the treatment plants are monitored centrally. This is performed by analysing partial streams.
- Waste gases and waste air are purified in scrubbers or absorption plants reflecting the current technological state of the art and are incinerated in flares or muffle furnaces as appropriate. Compliance of the outlets with the emission limit values is monitored as part of the requirements imposed by the supervisory authorities.
- Subsidiary streams from the processes are preferably recycled or disposed of in a suitable manner (thermal utilization, post-treatment in purification plant, transfer to dump).
- Storage containers for liquids are positioned in collecting trays or basins; diked areas are also utilised to contain any leaks from reaction vessels and transfer pipes.
- Environmental data and concentrations of hazardous substances are recorded by authorised personnel in compliance with legal requirements. The measurements are performed either by determining summation parameters or by tracking main components.
- Because of the intrinsic properties of the substance, local exhaust systems are provided as necessary for sampling, transferring and filling procedures.
- Plant Monitoring ensures that facilities comply with legal regulations (technical monitoring by in-house monitoring teams).
- Regular checking of facilities is performed by internal audits, supervisory authorities and independent experts.
(c) Only properly trained and authorised personnel handle the substance
- Operating instructions covering a wide range of topics (manufacturing instructions, operating instructions pursuant to Hazardous Substances Regulations) are updated at regular intervals as required.
- All facility employees receive plant-specific training before starting their activities. Regular follow-up training and instruction are provided on commencing new activities. Training sessions are documented in writing.
- External persons temporarily performing specific activities may only be authorised to perform the work if these persons have received special training for external personnel and if they have a written work permit specifying restrictions of time and location and a hazard assessment from the facility.
(d) In the case of cleaning and maintenance work, special procedures such as purging and washing are applied before the system is opened and entered
- Cleaning regulations are part of the standard operating and special instructions.
- Before opening a plant, it is rinsed, residual materials are emptied and the plant is dried if required. The state of the plant is documented (e.g. “in operation”, “residual materials emptied”, “rinsed and cleaned”). A work permit with hazard assessment may additionally be necessary.
- Inspections, maintenance activities and repairs require a work permit with hazard assessment; the employees performing these activities receive appropriate instruction.
- Depending on the result of the hazard assessment the type of personal protective equipment to be worn is specified.
(e) In cases of accident and where waste is generated, procedural and/or control technologies are used to minimize emissions and the resulting exposure during purification or cleaning and maintenance procedures
- Specialised personnel are permanently on standby to provide a competent, skilled damage containment response in case of accidents.
- The production processes are continuously monitored (in safety and environmental terms). If deviations from required conditions occur, but especially in case of damage, the facility management is informed with the aim of preventing or at least minimizing emissions
- In the case of leaks, possible sources are traced back to the process, or suitable, low-emission disposal pathways are used.
(f) Substance-handling procedures are well documented and strictly supervised by the site operator
- Various rules, instructions and regulations are available which are regularly revised and updated. They contain general guidance applicable for all employees as well as special instructions relating to substances, workplaces and activities:
- General rules of conduct and descriptions of protective measures based on the legal and employers’ liability insurance association’s safety, health and environmental protection regulations.
- Rules based on corporate guidelines and general rules of safety, health and environmental protection.
- Facility-specific rules for:
- -safe handling of equipment and machines
- -processes operated and
- -safe handling of all substances used
Process parameters of the complete production process are automatically recorded by the process control system and/or documented in batch records.
EHS (environmental protection, health and safety) performance is measured by RC (Responsible Care) audits in which potentials for improvement are identified and optimization measures implemented, as necessary.